Researchers look to expand market for cross-laminated timber
November 15, 2016
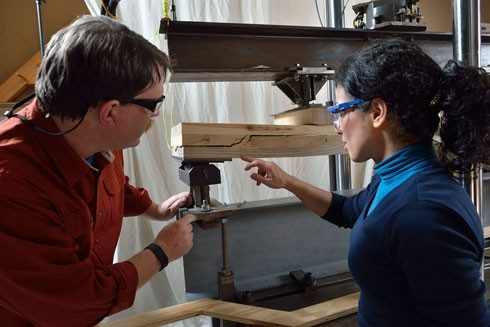
Associate Professor Daniel Hindman has researched high-performance wood composites for the better part of a decade. Four years ago, he seized the chance to help develop a material made from North American lumber that would be strong enough to replace concrete. Cross-laminated timbers (CLTs) are solid wood panels up to a foot and a half thick glued together from planks, like massive blocks of plywood. “The panels themselves are wood and glue, things we’ve had for a century,” Hindman said. “The innovation is in the concept, in thinking about the problem differently: how can we make a large-scale panel out of wood?”
To produce a CLT panel, pieces of lumber are placed side-by-side and glued together along the edges. The resulting sheets are then stacked with the grain perpendicular to the sheets above and below, spread with polyurethane or phenol formaldehyde — the same weatherproof, low-emitting adhesives used in plywood — and sandwiched together in a giant press. The panels can measure up to 10 feet wide, 50 feet long, and from four to 20 inches thick, depending on the number of layers.
The panels’ thickness and alternating grain pattern make buildings constructed with CLTs much stronger than traditional wood-frame structures. Designed to handle vertical and lateral loads, CLTs can be made to be stiffer and more stable than conventional wall systems. CLTs behave more like precast concrete: A single panel can form an entire section of wall, floor, roof, or even an elevator shaft without the need for additional structural support. CLT construction requires less energy and generates almost no onsite waste. In addition, CLTs weigh up to six times less than concrete, which reduces foundation costs.
Along with fellow faculty members in the Department of Sustainable Biomaterials, Hindman has designed CLTs from yellow poplar. He has also been working with the Southern Virginia Higher Education Center to study the use of southern pine CLTs. In the team’s tests, CLTs matched concrete’s performance in soundproofing and, perhaps surprisingly, fire resistance. “In a catastrophic fire, steel loses its tensile strength and collapses, and concrete cracks up, but wood beams this large will smolder and put themselves out,” said Department Head Bob Smith.
Hindman and Smith hope a plant will eventually open in Southwest Virginia. “We have to prove CLTs will work before anybody will invest in a plant,” Smith said. “Daniel’s research is helping us solve these issues.” Hindman is also researching with manufacturing variables, including the optimal amount of time in the hot press and the best treatments for adhesives, to help potential plant owners perfect their process quickly.
Read the full press release.