Wooden homes prefabricated in U.S. could help reduce housing deficit in Latin America
May 15, 2017
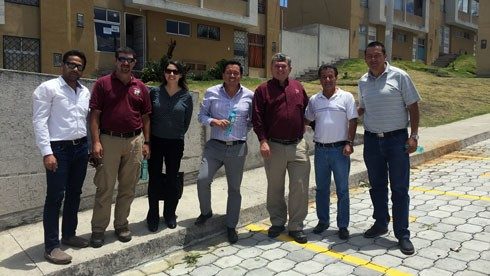
A research team from the Department of Sustainable Biomaterials is examining the market potential for wooden houses prefabricated in the U.S. as a way to help decrease the housing deficit in Latin America. These structures — which could be manufactured to specific international standards, packed in containers, and exported around the world — would provide affordable housing with low environmental impact and ease of construction.
The team, led by Associate Professor Henry Quesada, traveled to Peru, Ecuador, and Colombia to determine the market for, as well as the barriers to, using wood in residential and commercial structures. Master’s student Gaurav Kakkar explained that the local architects and engineers often do not have the background to create sustainable wooden structures. In addition, one of the biggest challenges is the cultural distrust of wooden structures’ ability to stand up against fire, earthquakes, or decay. However, this perception is changing following a 2016 earthquake in Ecuador, after which residents saw that most surviving structures were those made of wood.
In addition to helping remedy the global housing crisis, the development of the fabricated wood housing industry would be a boon for the “wood basket” region of the U.S. Southeast and Appalachians, thus increasing the region’s economy. “The opportunity to increase the export of higher value products such as prefabricated homes could mean an increase in economic development for the industry and specifically for rural areas where many jobs depend on the forest industry,” explained Professor Robert “Bob” Smith, co-principal investigator on the project.
The data collected during these visits will be used to develop a marketing handbook for manufacturers in the U.S. looking to export prefabricated wooden homes. The handbook will include both the marketing aspects and logistical issues related to the packaging, transportation, and installation of the structures.
Read the full press release.