Getting Down to Business: Wood Enterprise Institute Students Learn Entrepreneurship Firsthand
August 15, 2013
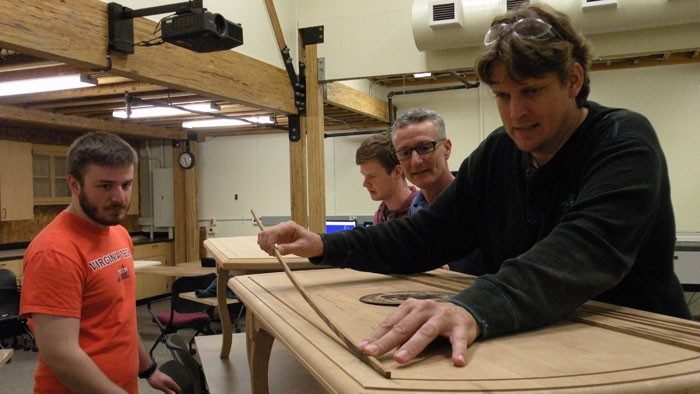
It’s the day before graduation — exams are finished, and the semester is essentially over. But a group of students still labors away in the Wood Enterprise Institute (WEI) lab at the Brooks Forest Products Center. They’re inlaying wood strips on tabletops, completing reports, and feeding instructions into a computerized milling machine.
The hands-on experience was by far the most exciting aspect.
“This may be the only class where students work more than required,” said senior Jeremy Withers of Christiansburg, Va., president of the student-managed entrepreneurial venture. “I’ve averaged 8-10 extra hours a week here; most of us have.”
Lured by the excitement of running their own business, using “cool” machines to create products, and being an integral part of a team, the students are putting theory into practice through experiential learning. And the experience isn’t just about the process, it has tangible benefits as well — virtually all WEI alums have jobs waiting for them after graduation.
“I learned that communication is very important,” said Andrew Corbin, a junior from Pennington, N.J. “You must make an effort to communicate with 17 other people to make them a team.”
“These students have to get things done through people,” said Professor Earl Kline, WEI’s faculty advisor. “They have to motivate others, keep them accountable, help them do their jobs. These are things they say they learned when the course is over.”
WEI is a concept-to-market venture run by the students as a two-semester course sequence. They design and develop prototypes of wood products, select one to produce, manufacture it in a sustainable manner, and sell it on the open market. Throughout the process, they learn to plan, delegate, and develop their leadership skills.
Past WEI teams have produced bookshelves, coasters, salt and pepper shakers, and decorative boxes. This year’s product design — an elegant coffee table with curved legs and inlaid wood designs created from the Henderson Lawn sycamore — was the most difficult a team has attempted, requiring precision machining on numerous parts. Modifications to improve product quality slowed production. The team produced fewer tables than planned, which significantly cut into the profit. “How the team responds to the challenges is where the true learning occurs,” said Kline.
Most WEI students are wood science and forest products majors, but few come in with advanced manufacturing skills. Fortunately, the college’s ongoing partnership with the Galway-Mayo Institute of Technology in Letterfrack, Ireland, one of Europe’s leading furniture design programs, has brought students to Blacksburg to complete their program’s on-the-job placement requirement. This past spring, Eoghan O’Connor was on hand to help the WEI team with the complexities of computer-aided manufacturing.
Kline initiated the WEI six years ago after searching unsuccessfully for a company willing to support students eager to try out new product ideas. “Companies aren’t set up to allow students to experiment, so Paul Winistorfer and I came up with the idea of allowing students to start their own business,” Kline said. “The WEI is about higher order learning,” Winistorfer added, “and encompasses critical thinking, problem solving, teamwork, and creativity as the basis for student learning.”
Enrollment in the WEI had remained fairly steady at about nine students, but doubled in the 2012-13 academic year. “Coordinating the work effort of so many students into effective results was a challenge, but it ended up being a tremendous learning experience for both the students and instructors,” Kline observed. “We are now better prepared to handle increased enrollment in the future.”
With financial assistance from donors, WEI has been able to buy materials and equipment, including software to run a CNC (computer numerical control) automated router that is the envy of most local woodworking companies. Donor Brooks Whitehurst, a 1951 Virginia Tech chemical engineering alumnus who holds 25 patents, attends the WEI presentations each year to give students critical feedback.
By the time the students deliver their final presentations, they have spent a collective hundreds of hours setting up their team structure, preparing a business plan, developing their product, writing computer code for the machinery, and creating marketing tools. This year they developed shop safety protocols that will be used by future WEI groups.
“The hands-on experience was by far the most exciting aspect,” said Michael Bauman, a senior from Marion, Va. “I don’t know of any other course in any major that allows students complete control of a business. Study of theory is necessary, but it doesn’t truly capture the raw excitement of actually solving problems in real scenarios.”